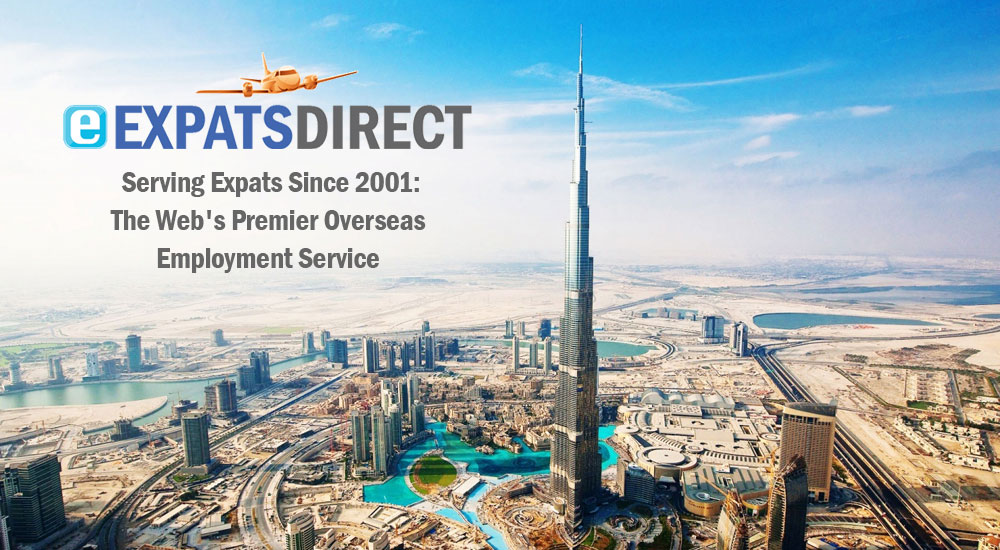
Freshest hand-picked jobs: View more jobs | Learn more
Senior Project Manager (Design Phase) | UAE | 03-Dec-24 |
Senior Resident Architect | UAE | 03-Dec-24 |
Senior Architect/Lead Architect | UAE | 03-Dec-24 |
Senior Site Architect | UAE | 03-Dec-24 |
Senior Contract Specialist | UAE | 03-Dec-24 |
Senior Irrigation Engineer | UAE | 03-Dec-24 |
Design Director - Interiors | UAE | 03-Dec-24 |
Associate (Interior Designer) - Dubai based | UAE | 03-Dec-24 |
Senior FF&E Designer | UAE | 03-Dec-24 |
Studio Director / Business Development Director (Interior) | UAE | 03-Dec-24 |
© All rights reserved, 2001 - 2025